Preparation
Material Preparation: The first step in grinding mica with Clirik's HGM Ultrafine Mill is to prepare the raw mica material. The mica should be crushed to a size of about 20mm using a jaw crusher. This initial crushing is crucial to ensure that the material can be effectively processed by the HGM mill. The crushed mica should be free of impurities and stored in a dry place to prevent moisture absorption, which can affect the grinding process.
Equipment Check: Before starting the grinding process, it is essential to thoroughly inspect all components of the HGM mill. This includes the grinding chamber, classifier, dust collector, and other key parts. Ensure that all components are securely fastened and in good working condition. Check for any signs of wear or damage, and replace any worn parts to prevent potential issues during operation.
Parameter Setting: Adjust the classifier speed according to the desired fineness of the mica powder. The HGM mill is capable of producing mica powder with a wide range of fineness, from 325 meshes to 2500 meshes. Properly setting the classifier speed is critical to achieving the desired powder fineness and ensuring efficient grinding.
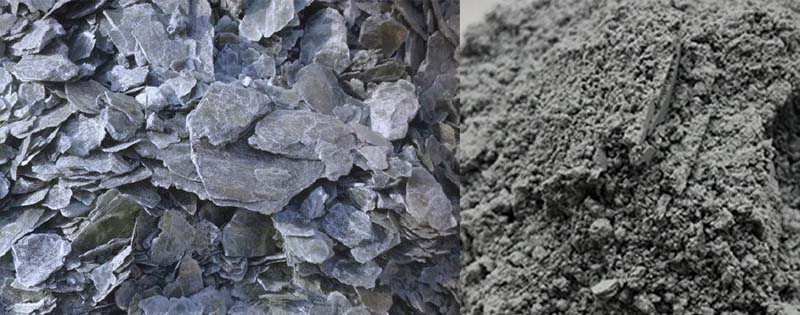
Grinding Process
Feeding: The crushed mica is fed into the grinding chamber using a vibrating feeder. The vibrating feeder ensures a consistent and even flow of material into the mill. This is important for maintaining a stable grinding process and achieving uniform powder fineness. The feeder should be adjusted to match the desired feeding rate, which may vary depending on the specific requirements of the grinding operation.
Grinding: Inside the grinding chamber, the mica material is ground into fine powder by the rotating rollers. The rollers apply significant pressure to the material, breaking it down into smaller particles. The grinding process is facilitated by the high-speed rotation of the turntable, which generates centrifugal force that pushes the material against the grinding rings. This combination of pressure and motion effectively reduces the mica to the desired fineness.
Classification: After grinding, the powder is carried by the airflow to the classifier. The classifier plays a vital role in separating the fine powder from coarser particles. The classifier's impeller spins at a high speed, creating a centrifugal force that separates the powder based on particle size. Coarser particles are returned to the grinding chamber for further grinding, while fine particles that meet the required fineness proceed to the next stage. This classification process ensures that only the desired fine powder is collected, resulting in a high-quality end product.
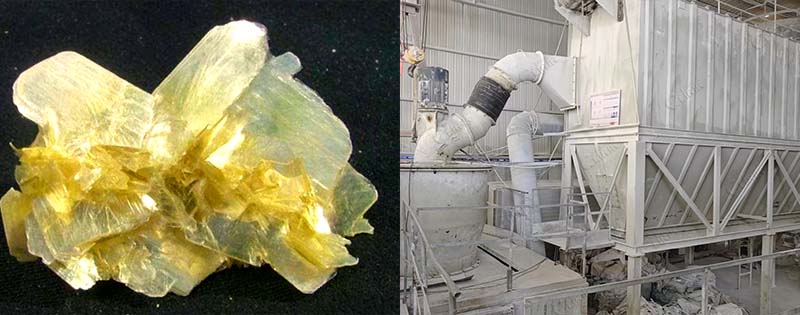
Collection and Packaging
Powder Collection: The fine mica powder is collected in a cyclone collector. The cyclone collector uses centrifugal force to separate the powder from the airflow. The collected powder falls into a collection bin or bag, ready for packaging. It is important to regularly check the cyclone collector to ensure that it is functioning properly and that the collected powder is of the desired quality.
Dust Cleaning: Any residual dust from the grinding process is removed by the dust collector. The dust collector helps to maintain a clean and safe working environment by capturing and removing fine dust particles. Regular maintenance of the dust collector is essential to ensure its effective operation and to prevent dust buildup, which can affect the overall efficiency of the grinding process.
Packaging: The collected mica powder is then packaged for storage or transportation. The packaging should be appropriate for the intended use of the powder and should protect it from moisture and contamination. Proper packaging ensures that the mica powder remains in good condition until it is ready for use.