Shanghai Clirik Machinery has introduced its HGM Grinding Mill, which efficiently converts raw calcite into ultra-fine powder. This mill meets the strict requirements of various industries and is known for its efficiency, precision, advanced technology, and eco-friendly design.
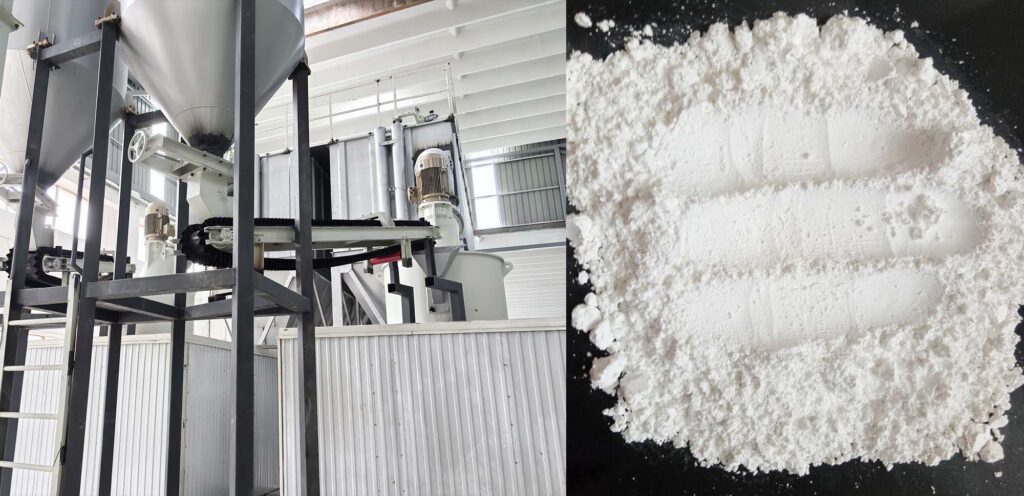
Advanced Design for High-Quality Output
The HGM Grinding Mill is a testament to modern engineering, designed to produce high-quality calcite powder with remarkable efficiency. Its ability to adjust the final product fineness between 150 and 3000 mesh (74-5 microns) makes it highly versatile, catering to a wide range of industrial applications. This flexibility is crucial for industries that require precise control over powder fineness to ensure optimal performance of their products.
Detailed Working Principle
The HGM Mill operates through a series of meticulously designed steps to ensure the production of high-quality calcite powder:
Material Feeding: Raw calcite is first crushed by a hammer crusher to reduce its size. The crushed material is then transported to a storage hopper via an elevator. A vibrating feeder ensures an even supply of material into the upper distribution plate of the turn plate through a sloping feeding pipe. This consistent feeding is crucial for maintaining the efficiency of the grinding process.
Grinding Process: The main bearing and each dial of the mill are driven by an electromotor through a reducer. This mechanism causes the grinding rollers to roll and rotate within the ring channels. The material is driven to the edge of the turn plate by centrifugal force and falls into the grinding chambers, where it is crushed and ground into fine powder. The grinding process is carefully controlled to achieve the desired fineness of the powder.
Classification and Collection: The high-pressure air blower constantly inhales air, creating an airflow that carries the crushed material to the classifier. The high-speed impeller of the classifier screens the airflow: unqualified particles fall back into the mill for regrinding, while qualified particles mix with air and enter the cyclone powder collector. Most of the qualified powders fall and exit from the discharging valve at the bottom of the cyclone collector. A small proportion of fine powders moves to the dust cleaner, ensuring that only particles of the desired fineness are collected.
Final Packaging: The collected powders are transported by a conveyor belt for packaging. The packaged powder is then ready for shipment to customers worldwide. This final step ensures that the high-quality calcite powder reaches the market in a timely and efficient manner.
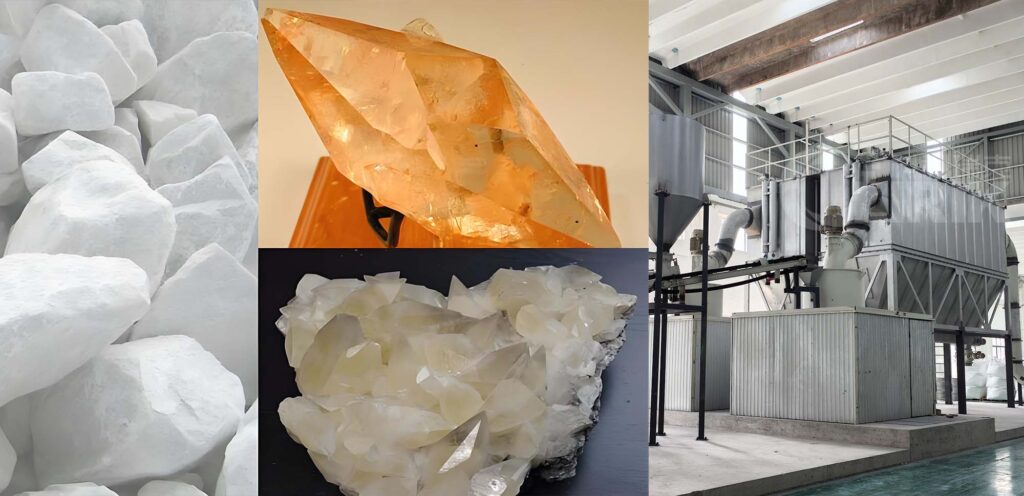
Versatile Applications of Calcite
Calcite is a versatile non-metallic mineral with a wide range of applications due to its unique physical and chemical properties. In the construction industry, calcite powder is a key ingredient in paints, coatings, and adhesives, enhancing their performance and durability. In the chemical industry, it serves as a raw material for the production of calcium carbonate, which is crucial for manufacturing plastics, rubber, and paper. In the pharmaceutical industry, calcite powder is used as an excipient in drug formulations, providing stability and improving the bioavailability of active ingredients. Additionally, in the cosmetics industry, calcite powder is valued for its ability to provide a smooth texture and enhance the appearance of cosmetic products.
Key Features and Advantages
The HGM Grinding Mill is designed to offer unparalleled performance in calcite powder production. Some of its key features include:
High Efficiency: The HGM Grinding Mill achieves twice the capacity of traditional jet mills, mixing grinders, and ball mills under the same motor power and finished size, while reducing energy consumption by up to 30%.
Flexible Fineness Adjustment: The final product fineness can be precisely adjusted between 150 meshes and 3000 mesh (74-5 microns), catering to a wide range of industrial requirements.
Long Lifecycle of Spare Parts: The specially forged ring and roller materials provide a lifespan of about one year, which is 2-3 times longer than that of impact or turbo mills. For calcite carbonate, the lifespan can extend to 2-5 years, depending on material hardness.
Advanced Intelligent Speed Control: This feature enables even material feeding and stable fineness by adjusting the main speed to suit the ground material. The intelligent control system enhances capacity and efficiency while reducing power consumption, ensuring consistent performance.
Environment-Friendly: The mill incorporates pulse bag filters and mufflers to minimize dust pollution and noise. This design ensures compliance with modern green production standards, making the HGM Grinding Mill a sustainable choice for environmentally conscious manufacturers.
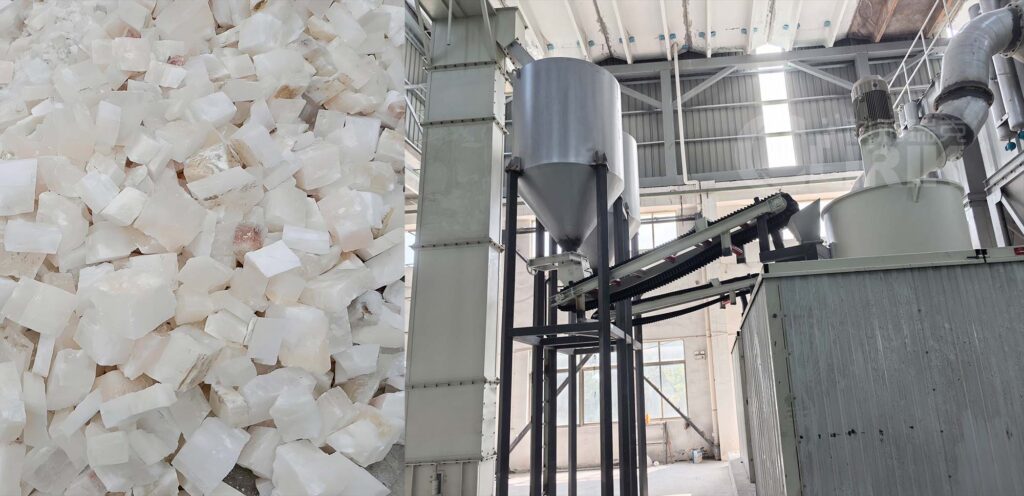
Global Impact and Future Prospects
The introduction of the HGM Grinding Mill has revolutionized calcite powder production by offering a highly efficient, precise, and environmentally friendly solution. Clirik’s commitment to continuous innovation and customer support ensures that the mill remains at the forefront of the industry. With its ability to meet the stringent requirements of various industries, the HGM Grinding Mill is poised to drive further growth and development in the global calcite market. As the demand for high-quality calcite powder continues to rise, Shanghai Clirik Machinery’s HGM Grinding Mill stands out as a reliable and innovative choice for producers worldwide. By leveraging advanced technology and sustainable practices, Clirik is paving the way for a more efficient and eco-friendly future in mineral processing. The company’s dedication to R&D and customer satisfaction ensures that the HGM Grinding Mill will continue to evolve and meet the changing needs of the market.